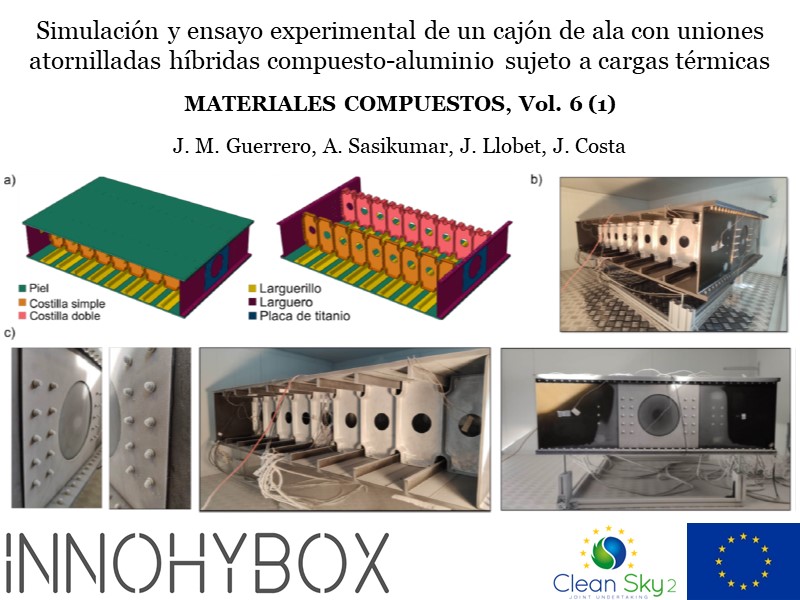
25 Mar New paper on simulation and experimental testing of a bolted carbon-aluminium hybrid wingbox assembly under thermal loads
The paper entitled “Simulación y ensayo experimental de un cajón de ala con uniones atornilladas híbridas compuesto-aluminio sujeto a cargas térmicas” (Simulation and experimental testing of a bolted carbon-aluminium hybrid wingbox assembly under thermal loads) has been recently published by José Manuel Guerrero García and other AMADE researchers as co-authors. The paper has been published at the AEMAC journal, “Materiales Compuestos”, volume 6 (1), pages 63-74 and is available at the following link:
https://revista.aemac.org/materiales-compuestos/article/view/531
On the last decades, the aeronautical industry has increased the use of Carbon Fibre Reinforced Polymer matrix composites (CFRP), and at the same time, has kept the use of conventional metals. This has led to the presence of hybrid assemblies in the wingbox, fuselage, etc. Due to their high stiffness and strength, as well as the ease to disassemble and repair, these assemblies are usually bolted. During its usage, an aircraft is subjected to large thermal jumps (the temperature difference between a landed aircraft and a flying one can reach 140 ºC). Because of the presence of hybrid bolted joints, the materials of the joint undergo different thermal expansion/contraction, which cause significant thermal stresses altering the mechanical behaviour of the joint.
Framed in the aeronautical Clean Sky 2 project ‘INNOHYBOX’, this work studies the behaviour of hybrid bolted joints subjected to thermal loads, both numerically and experimentally, following a pyramidal approach. At the coupon level, a hybrid carbon-aluminium single-lap shear specimen with one bolt was used to comprehend and characterise its behaviour under thermal loads. At the substructural level, a subcomponent representative of a wingbox was tested under thermal conditions. Finally, a full wingbox was tested. Furthermore, a computationally efficient finite element model was developed to simulate the complex behaviour of these type of joints without compromising the computational cost. The numerical predictions correlate favourably against the experimental data.
This work has been carried out within the framework of the EU H2020 Clean Sky 2 INNOHYBOX project -Innovative solutions for metallic ribs or fittings introduced in a composite box to optimally deal with thermo-mechanical effects, of the Clean Sky 2 Joint Undertaking (JU) program under Grant Agreement No. 785433.