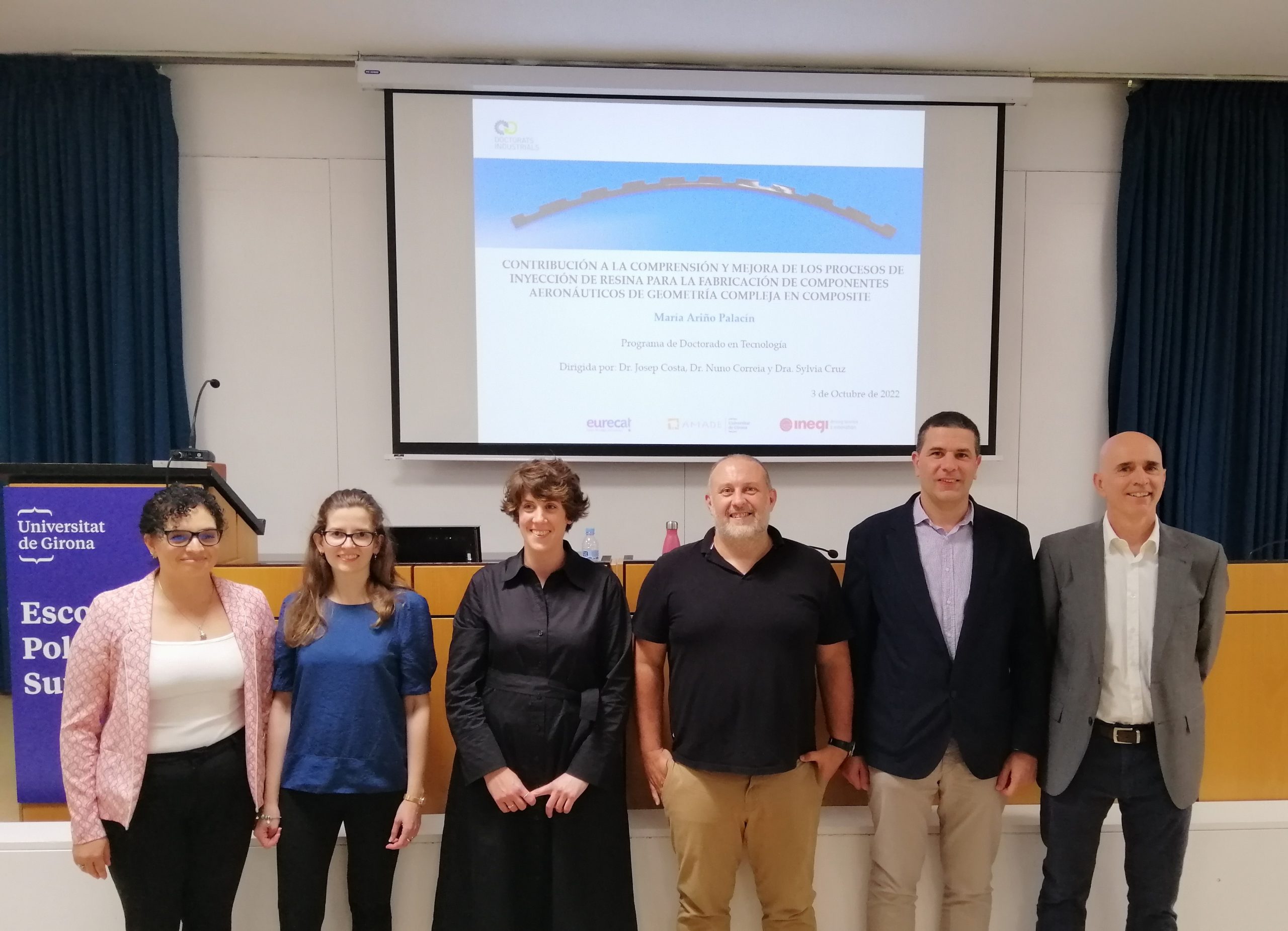
05 Dic Doctoral thesis on Liquid Composite Moulding (LCM) processes for the manufacture of aeronautical components of complex geometry in composites
Maria Ariño Palacín defended her PhD thesis entitled “Contribution to the understanding and improvement of resin injection processes for the manufacture of aeronautical components of complex geometry in composites” on October 3, 2022. The PhD advisors of the doctoral thesis are Prof. Josep Costa (AMADE – UdG), Dr. Nuno Correia (INEGI) and Dra. Sylvia Cruz (EURECAT).
The aeronautic industry indeed uses composites and, the application on designing large dimension complex structures is emerging. The autoclave process is the technology used by default, considering the high repeatability process and the high-performance parts. However, replacing this process with more sustainable ones like Liquid Composite Moulding (LCM), is desirable and is achieving gradually in the aviation. In this thesis, the research is focus on the development of the RTM process and the vacuum infusion process to manufacture primary fuselage structures that meet the aeronautical sector requirements. In regards of vacuum infusion process, the work describes the modification of the vacuum infusion process based on the application of an external pressure on the vacuum bag. External pressure is applied through a solid incompressible counter-mould, which may or may not incorporate couplings made of materials that are more rigid or more flexible than the counter-mould itself. The application of external pressure on the incompressible counter-mould has shown an increase in the compaction of the laminate, especially in the areas of high curvature and the disappearance of the bridging effect. In the case of RTM, we provide a work methodology that allows us to conceive the process on an industrial scale to manufacture high-quality aeronautical parts. To do this, we used a holistic strategy that covered both the injection and post-filling phases, as well as the design of the mould, raw material selection and the process parameterization.
The thesis has been developed within the Industrial Doctorate Plan program of the Catalan government, in collaboration with the University of Girona and the Eurecat Tech Center. Part of this research has also been funded by the European Clean Sky Joint Undertaking (CSJU) program in accordance with the project COFRARE 2.0 (H2020-CS2-CFP02-2015-01) and with the support the Alenia Aeronautica S.p.A, as a Topic Manager. This has also been complemented by an international stage at the Institute of Science and Innovation in Mechanical and Industrial Engineering (INEGI) in Porto (Portugal).
The Doctoral Degree includes industrial and international mention.